自動車部品メーカー各社がカーボンニュートラル(CN、温室効果ガス排出量実質ゼロ)に向けて思考を巡らせ、技術を磨いている。世界各国・地域で脱炭素に関する規制が強化されることはもちろん、CNを実現できないと取引対象から除外されたり、「ペナルティー」として費用を加算されたりする可能性もあり、競争力や収益に直接影響しかねない。もはやCNは単なる目標ではなく、乗り越えるべき喫緊の課題となっている。
デンソー福島 ラジエーターの高温接合を電化
部品メーカーの間では二酸化炭素(CO2)の排出量を実質ゼロ、もしくは大幅に低減した製品を供給する事例が増え始めている。デンソーもその1社だ。生産子会社のデンソー福島(福島県田村市)で手がける自動車部品「ラジエーター」でCNを実現。トヨタ自動車東日本(TMEJ、宮城県大衡村)に納品を始めた。
同ラジエーターではアルミニウム製の部品を高温で接合する工程がある。CNの取り組みでは同工程を電化。また同工程で排出されるガスを燃焼させて無害化する「アフターバーナー炉」の燃料についても、液化石油(LP)ガスから水素に切り替えた。水素はデンソー福島の敷地内に設置した、トヨタ自動車製の水電解装置で生成する。
デンソーとして同ラジエーターは、再生可能エネルギーの購入をせずにCNを実現した第1号の製品となった。外部調達した再生エネを使うことなく、地産地消の水素や電力を活用しCNを達成。同社はこの工程を「ショーケース」と位置付け、CNを目指す他の製造業などにも公開する方針だ。山崎康彦デンソー副社長は「水素利活用の仲間の輪を広げ、福島から全国へ、水素地産地消モデルを展開したい」と意気込む。
トヨタ紡織も新工法によるCO2排出量低減に取り組む。車の電動化対応製品として刈谷工場(愛知県刈谷市)で生産する車載モーター用「モーターコア」の工程の一部で熱可塑性樹脂を使用。加熱や冷却工程を廃止しCO2排出量を従来比98%削減した。
豊田合成では植物を原料としたセルロースナノファイバー(CNF)を配合した新たな樹脂の開発を進めている。原料に植物を使用することで、植物が育つ過程で吸収した分のCO2と廃棄に必要なCO2を相殺。CO2の総量が増えないメリットがある。
同社が開発した新樹脂は自動車用のバンパー、フードとなり、このほどトヨタの高級車ブランド「レクサス」の水素エンジンを搭載したコンセプトバギー(小型オフロード車)「ROV」に採用された。25年の量産化に向けてさらに技術を磨く。
曙ブレーキ ブレーキパッド工程省略
独立系の曙ブレーキ工業は、製造過程のCO2発生量を従来比で半減できるブレーキパッドを開発した。原材料の一部の変更などにより、ブレーキパッドを焼き固める工程のうち、特に高温となる工程を省くことなどで実現。製造時間も半分以下に短縮可能だ。
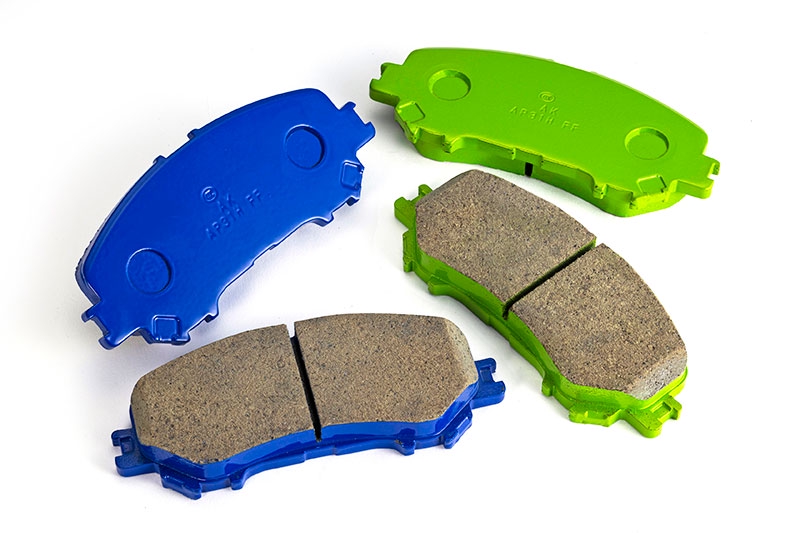
同社の宮地康弘社長は完成車メーカーが部品を選ぶ基準として「(直接取引する)サプライヤー(仕入れ先)がCO2をどこまで削減できているかを重要視している」と状況を説明する。その上で「今度は我々のようなサプライヤーと取引する、さらにティア(階層)の深いサプライヤーが排出するCO2についても気にするようになってきている」と強調する。
豊田織機 フォーク用水素充填所設置
生産工程だけでなく物流の領域でもCN実現に向けた動きが加速している。豊田自動織機はフォークリフトの基幹工場である高浜工場(愛知県高浜市)で、燃料電池フォークリフト用の水素充填所「H2プラザ」を設置している。再生エネである太陽光から生み出した電力だけを用いて水素を製造・圧縮・蓄圧する。燃料電池フォークリフトにこの水素を供給することで、水素の製造から燃料電池フォークリフトによるモノの移動までの一連の流れでCO2を排出しない環境を構築した。
20年ごろから本格的に浸透し始めたCN実現の取り組み。当初は「50年にCO2排出量ゼロ」や「中間段階として30年までにCO2排出量を半減」といった数値目標は厳しいハードルと思われていたものの、各社の意欲的な技術開発や創意工夫が功を奏し、目標達成が現実味を帯びつつある。
完成車拠点の燃料転換進む 鋼材もグリーン対応
完成車メーカーでもCNに向けた取り組みが着々と進む。
マツダは広島の本社工場の発電について、石炭からアンモニア専焼に燃料転換する方針を示している。四国電力や三菱商事などと共同で、波方ターミナル(愛媛県今治市)をアンモニアを取り扱う中核拠点にする計画が進行中。同拠点から内航船でマツダ本社工場にアンモニアを輸送する想定だ。アンモニア専焼への転換は30年を見据え、新たな発電設備を建設する。太陽光発電による電力の活用や再生エネの購入といった施策も絡めて、マツダの国内自社工場・事業所の非化石電気使用率は30年度時点で75%に高まる見通しだ。
日産自動車は神戸製鋼所が商品化した低CO2高炉鋼材「コベナブルスチール」や、太陽光発電の電力で電解製錬しCO2排出量を半減したグリーンアルミ原料を用いたアルミ板材を順次適用していく。車両重量の約60%は鉄部品、約10%はアルミ部品で構成されており、製造時のCO2排出削減に直結する取り組みとして推進する。
【関連記事】 デンソーも注目、岐阜の「改革マスター」とは?